Kemp Co., Ltd Introduction to Kemp Technology's Excellence in the Engi…
관리자 25-02-05 14:50
페이지 정보
본문
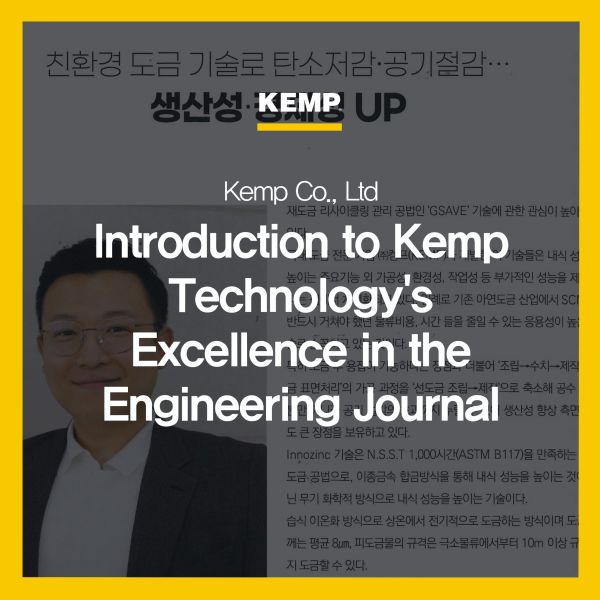
In June 2024, in the Engineering Journal
Introducing Kemp's Excellent Technology
Engineering Journal is the only engineering comprehensive magazine in Korea consisting of professional journalists in each field of engineering.
Kemp's excellent eco-friendly plating technology was introduced in the engineering journal in June 2024.
Carbon reduction and air reduction with eco-friendly plating technology
Productivity/Economy UP
In line with the recent carbon emission reduction paradigm, the plating technology of the steel industry, which is the traditional root industry, is expected to be replaced by eco-friendly technology. In line with the steel industry's eco-friendly strategy, which has been considered the main culprit of environmental pollution, eco-friendly technologies such as carbon-free zinc surface treatment technology have begun to be applied in the plating process.
In particular, there is growing interest in "Innozinc," a ceramic galvanizing technology that can replace the existing carbon multi-emission hot-dip galvanizing method, and "GSAVE," an aging hot-dip galvanizing guardrail site re-plating recycling management technology.
These technologies, developed by KEMP, a domestic plating company, are differentiated in that they provide additional performance such as processability, environmentality, and workability in addition to major functions that increase corrosion resistance. For example, in the existing galvanizing industry, it is regarded as a highly applicable technology that can reduce logistics costs and time that must be gone through in SCM.
In particular, in addition to the advantage of being able to weld after plating, the processing process of "assembly → numerical → manufacturing → plating surface treatment" can be reduced to "preparation → manufacturing", which has a great advantage in terms of productivity improvement as well as air quality reduction.
Innozinc technology is a galvanizing method that satisfies 1,000 hours of N.S.S.T. (ASTM B117), and it is a technology that increases corrosion resistance in an inorganic chemical method rather than increasing corrosion resistance through a dissimilar metal alloy method.
The wet ionization method is an electric plating method at room temperature, and the plating thickness is 8 μm on average, and the standard of the coating material can be plated from minimal logistics to a scale of 10m or more.
In addition, it is an appropriate technology that is not only superior to the existing plating method after plating, but also has about 5-10% cheaper economic feasibility than hot-dip galvanizing in terms of cost, and can reduce carbon emissions by about 64% compared to hot-dip galvanizing based on the same size facility.
In addition, GSAVE technology, one of Kemp's representative technologies, is a management method that improves corrosion resistance by filling and re-receiving the installed hot-dip galvanized iron structure with zinc on site.
Kemp is continuing its business by targeting guardrails, which are the most extensive among iron structures and are easy to apply applications first. In addition, it is seeking to apply facilities that are in the blind spot of management after the construction of transmission towers, lighting towers, and soundproof walls.
In particular, in most cases, guardrails are not managed within the installation period after the maintenance period of 5 years after installation is over. The installation period is an average of 20 to 30 years, and there are cases where they are placed in the blind spot of management for at least 15 to 25 years.
Accordingly, Kemp developed GSAVE technology as a management method for hot-dip galvanized iron structures between installation and replacement. GSAVE's process is as follows.
First of all, the corrosion of the structure is detected and analyzed through an object recognition algorithm to select a pretreatment method and coating thickness that can minimize the impact on the field environment. Accordingly, Kemp's environmentally friendly technologies are applied to remove tire dust and pollutants from the guardrail surface.
After that, inorganic chemistry-based room temperature cured zinc flake coating is carried out, and about 20 to 25 μm of zinc (about N.S.S.T. 3,000h) is replenished in the field. Existing solvent-type coatings have properties that are vulnerable to UV, but Kemp's GSAVE solution can secure continuous corrosion resistance after drying and water resistance, odorless, and curing within 24 hours of room temperature within 10 minutes of application.
Based on this, it solves problems such as replacing damaged guardrails and fastening bolts, and safely manages widely installed steel structures. GSAVE technology is also evaluated as a technology capable of 70% national treasury reduction and 99.6% carbon emission reduction compared to the installation of new guardrails after demolition.
"Kemp is a technology company that has all environmentally friendly corrosion solutions according to the life cycle of iron based on inorganic chemical technology," said CEO Jeon Hyun-joon. "It has original technology and process technology ranging from iron pretreatment to temporary rust prevention, plating and coating, post-treatment, and repair, and corrosion technology of non-ferrous metals such as aluminum and magnesium."
Kemp's technology is currently being applied by replacing existing technology by changing technical standards in various industries. Until recently, KS standards have been changed and eight association standards have been completed, and hot-dip galvanizing has been changed to ceramic galvanizing technology based on 13 specifications standards for large domestic and foreign companies.
Currently, the Kemp Ulsan plant operates a 17,000-ton plating facility that can replace small-sized iron logistics and large-sized iron appliances with Innozinc, which were previously surface-treated with molten galvanizing, and many iron logistics samples are mass-produced after testing and mass production in various industries.
CEO Jeon said, "In the recent plating market, Innozinc (ceramic galvanizing) technology is being rapidly applied to various industries. However, we expect problems with copy products to occur when applying technology to emerging markets, and we are currently conducting DX conversions with various institutions to collect and manage manufacturing data and expand into the plating service business through digital conversion. We are establishing and progressing strategies for advanced processes and modularizing factories to keep pace with changes in the working environment such as a shortage of manpower in the future."
He continued, "The problems caused by carbon emissions cannot be ignored by industry and economic logic.
Introducing Kemp's Excellent Technology
Engineering Journal is the only engineering comprehensive magazine in Korea consisting of professional journalists in each field of engineering.
Kemp's excellent eco-friendly plating technology was introduced in the engineering journal in June 2024.
Carbon reduction and air reduction with eco-friendly plating technology
Productivity/Economy UP
In line with the recent carbon emission reduction paradigm, the plating technology of the steel industry, which is the traditional root industry, is expected to be replaced by eco-friendly technology. In line with the steel industry's eco-friendly strategy, which has been considered the main culprit of environmental pollution, eco-friendly technologies such as carbon-free zinc surface treatment technology have begun to be applied in the plating process.
In particular, there is growing interest in "Innozinc," a ceramic galvanizing technology that can replace the existing carbon multi-emission hot-dip galvanizing method, and "GSAVE," an aging hot-dip galvanizing guardrail site re-plating recycling management technology.
These technologies, developed by KEMP, a domestic plating company, are differentiated in that they provide additional performance such as processability, environmentality, and workability in addition to major functions that increase corrosion resistance. For example, in the existing galvanizing industry, it is regarded as a highly applicable technology that can reduce logistics costs and time that must be gone through in SCM.
In particular, in addition to the advantage of being able to weld after plating, the processing process of "assembly → numerical → manufacturing → plating surface treatment" can be reduced to "preparation → manufacturing", which has a great advantage in terms of productivity improvement as well as air quality reduction.
Innozinc technology is a galvanizing method that satisfies 1,000 hours of N.S.S.T. (ASTM B117), and it is a technology that increases corrosion resistance in an inorganic chemical method rather than increasing corrosion resistance through a dissimilar metal alloy method.
The wet ionization method is an electric plating method at room temperature, and the plating thickness is 8 μm on average, and the standard of the coating material can be plated from minimal logistics to a scale of 10m or more.
In addition, it is an appropriate technology that is not only superior to the existing plating method after plating, but also has about 5-10% cheaper economic feasibility than hot-dip galvanizing in terms of cost, and can reduce carbon emissions by about 64% compared to hot-dip galvanizing based on the same size facility.
In addition, GSAVE technology, one of Kemp's representative technologies, is a management method that improves corrosion resistance by filling and re-receiving the installed hot-dip galvanized iron structure with zinc on site.
Kemp is continuing its business by targeting guardrails, which are the most extensive among iron structures and are easy to apply applications first. In addition, it is seeking to apply facilities that are in the blind spot of management after the construction of transmission towers, lighting towers, and soundproof walls.
In particular, in most cases, guardrails are not managed within the installation period after the maintenance period of 5 years after installation is over. The installation period is an average of 20 to 30 years, and there are cases where they are placed in the blind spot of management for at least 15 to 25 years.
Accordingly, Kemp developed GSAVE technology as a management method for hot-dip galvanized iron structures between installation and replacement. GSAVE's process is as follows.
First of all, the corrosion of the structure is detected and analyzed through an object recognition algorithm to select a pretreatment method and coating thickness that can minimize the impact on the field environment. Accordingly, Kemp's environmentally friendly technologies are applied to remove tire dust and pollutants from the guardrail surface.
After that, inorganic chemistry-based room temperature cured zinc flake coating is carried out, and about 20 to 25 μm of zinc (about N.S.S.T. 3,000h) is replenished in the field. Existing solvent-type coatings have properties that are vulnerable to UV, but Kemp's GSAVE solution can secure continuous corrosion resistance after drying and water resistance, odorless, and curing within 24 hours of room temperature within 10 minutes of application.
Based on this, it solves problems such as replacing damaged guardrails and fastening bolts, and safely manages widely installed steel structures. GSAVE technology is also evaluated as a technology capable of 70% national treasury reduction and 99.6% carbon emission reduction compared to the installation of new guardrails after demolition.
"Kemp is a technology company that has all environmentally friendly corrosion solutions according to the life cycle of iron based on inorganic chemical technology," said CEO Jeon Hyun-joon. "It has original technology and process technology ranging from iron pretreatment to temporary rust prevention, plating and coating, post-treatment, and repair, and corrosion technology of non-ferrous metals such as aluminum and magnesium."
Kemp's technology is currently being applied by replacing existing technology by changing technical standards in various industries. Until recently, KS standards have been changed and eight association standards have been completed, and hot-dip galvanizing has been changed to ceramic galvanizing technology based on 13 specifications standards for large domestic and foreign companies.
Currently, the Kemp Ulsan plant operates a 17,000-ton plating facility that can replace small-sized iron logistics and large-sized iron appliances with Innozinc, which were previously surface-treated with molten galvanizing, and many iron logistics samples are mass-produced after testing and mass production in various industries.
CEO Jeon said, "In the recent plating market, Innozinc (ceramic galvanizing) technology is being rapidly applied to various industries. However, we expect problems with copy products to occur when applying technology to emerging markets, and we are currently conducting DX conversions with various institutions to collect and manage manufacturing data and expand into the plating service business through digital conversion. We are establishing and progressing strategies for advanced processes and modularizing factories to keep pace with changes in the working environment such as a shortage of manpower in the future."
He continued, "The problems caused by carbon emissions cannot be ignored by industry and economic logic.
댓글목록
등록된 댓글이 없습니다.